Most bikers have NO clue what's going on inside their shocks, and no idea how to adjust them. That's OK if you're a gutter bunny -- you probably don't need shocks anyway. But if you're going to hit some real rock, adjusting your shock absorbers can make the difference between "terrified-newbie" and "god-on-two-wheels."
Shocks can do two things: (1) They let the wheel move up when it hits something, without forcing the bike and rider to take a similar violent motion. To do this, the wheel is suspended on something springy. This can be a metal spring, compressed air, or a rubbery substance (elastomer). The amount of springiness is called "preload." (2) The shock can control the speed of the axle motion, both when the wheel takes the hit, and when it rebounds to its original position. This is called "dampening." This is a second system in the shock -- usually a hole through which fluid or air is forced as the shock absorber moves. The size of the hole determines how much the shock resists shortening or lengthening.
The type of shock determines how it responds to changing conditions. For example, an elastomer shock will feel stiffer during cold winter rides, while a compressed-air shock will feel a bit softer when it's cold. Dampening increases with cold (the fluid gets "stiffer"), so the rebound of the shock will be slower in the winter.
Some shock absorbers have an additional feature called "lock out." This freezes the shock so it can't move. Why would you want to have NO shock absorption? Because it can make the bike more efficient during a long climb.
On this rear shock, air is being added through the high-pressure port. The red disc is the rebound dampening dial. It determines how fast the wheel moves after absorbing a hit. The blue lever is a "lock-out," which freezes the shock so the bike performs like a hardtail. The ring at the bottom is part of the "attitude adjustment." By turning the shock on the threads of the mounting, you can move the rear wheel up or down, changing the angle of the bike.
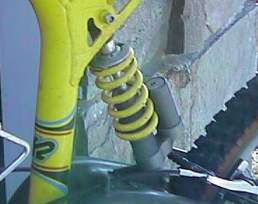
In the center of the spring is the rebound dampening unit. Fluid flows within the shock absorber as it changes length. Increasing the resistance to flow increases the "dampening," so the bike isn't as "bouncy." (This shock does NOT have a lock-out. It's always working.)
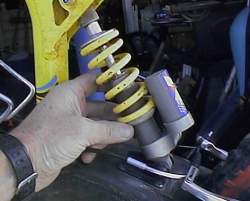
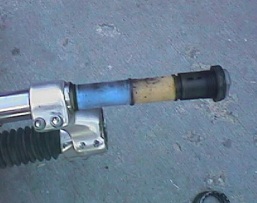
An elastomer shock can be made stiffer by pre-compressing the material. When the knob at the top is turned, it screws a second sleeve down, pushing the elastomer down and increasing the tension within the shock.
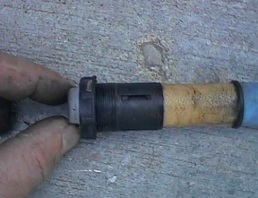
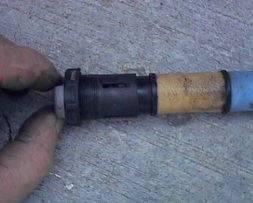
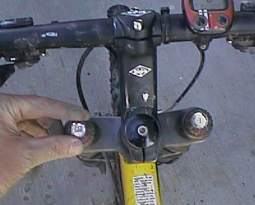
On these shocks, the dial on one side controls the preload (bounce or stiffness). The dial on the other side controls the speed of motion (dampening). On this shock, the left side is dampening, the right is preload.
Periodically, check the dampening by turning it up full. If you don't detect significant slowing of the rebound when you compress the shock, the shock needs service. It may be out of oil, or it may have an internal malfunction.
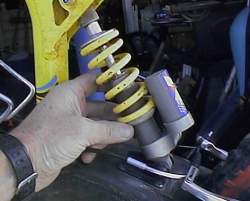
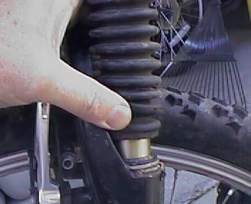
Clean off the outside of the boot with a degreasing wash. Now pull up the boot from below. Wipe off the boot mount. Clean the inside edge of the bottom of the boot sleeve with a cotton swab.
Apply a thin coating of bearing grease to the shaft of the shock. If your boot has a shaft-hugging top edge (as shown), run a thin layer of bearing grease around the inside of the top of the boot. Reattach the boot.
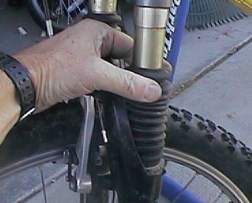